
The white lines that appear between wood board edges of site-applied finishes on wood floors is commonly known as White Line Syndrome, or WLS. This issue can be a headache for contractors because it ruins the overall look of the floor and needs to be
dealt with. There are a few reasons why WLS can occur on wood floors. Continue reading to learn more and how to keep it from happening.
Trapped Solvents
Solvents from stains and finishes that are trapped and unable to evaporate can lead to WLS. Although both oil-based and waterbased stains can pool in between boards, cracks, seams, butt-joints, or filled knot holes, oil-based stain takes a much longer
time to dry completely. Waterbased stains dry quicker than oil-based stains because water evaporates faster than oil. Oil-based stains, sealers, and finishes also generally contain more solvents than waterbased products. In addition, coating a floor
with finish before the solvents from a previously applied product have evaporated will trap them, causing WLS and cloudy lines between wood boards.
To help with the drying process and to ensure stains and finishes are completely dry, use strategically placed fans pointed at the wet floor. Creating a good airflow across the surface of the floor helps accelerate the drying process. Good ventilation
is crucial during any wood floor project to help with the drying phase. There are a few tricks to determine if floor stain or finish has dried. Traditionally, a contractor might take a white rag, wipe the floor and see if any color from the stain
is pulled onto the rag. This strategy tests the dryness of the floor surface, but it does not work for the gaps in the floor. Try using a vacuum test in several locations of the wood floor to see if any liquid is pulled to the surface. Simply
add a white rag on the end of a vacuum hose and see if any liquid/stain in the tongue-and-groove of soft grains areas of the wood can be pulled up. If liquid is pulled, the floor needs more time to dry. Test if the floor finish is dry by using
a moisture meter and/or feeling the floor. If the moisture meter achieves the readings required, or if the finish does not move or leave any marks from your hand, it has dried enough.
Moisture
The wood’s Equilibrium Moisture Content (EMC) is critical to reaching a point of balance with humidity in the environment. With more humidity in the air, the wood will absorb the moisture and expand. With less, it will release moisture and induce
shrinkage, resulting in gaps between the floorboards. Once the wood reaches its EMC, it will stabilize and changes in the wood will cease. However, if the humidity in the environment shifts drastically, the EMC will become unstable, and finishes
may stretch over resulting gaps instead of breaking, causing the white lines to appear.
Utilize a wood moisture meter to check the wood for excessive moisture before applying coatings to reduce the risk of WLS. Post-application issues, such as leaks or improper maintenance, can also affect EMC and cause WLS. The use of steam mops, for
example, will force vapor moisture into and between boards. Read more about how temperature and humidity can affect a wood floor.
"Once WLS appears on a floor, the only option is to treat it. "
Loss of Adhesion
When a wood floor experiences vertical or lateral movement between boards, finish may begin to lose adhesion and turn white. It can also start chipping or peeling. Peeling can be the source of other problems as well. Read more about peeling here.
Adhesion issues can occur when finishes are used over oil-based stains or previous coatings that have not dried or cured sufficiently. Contamination between the seams of the boards and poor inter-coat abrasion along the edges of adjoining boards result
in finish adhesion failure and WLS. As previously mentioned, making sure the floor is dry will help prevent adhesion issues and WLS.
Cures for WLS
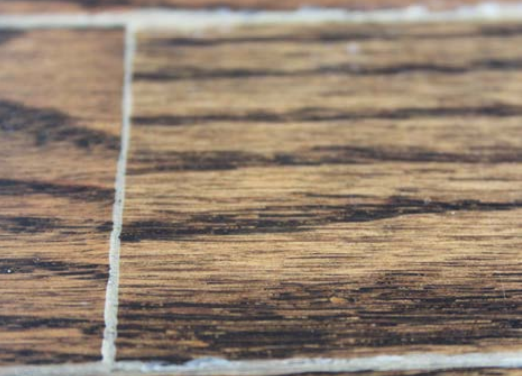
Once WLS appears on a floor, the only option is to treat it. If the finish appears to be stretching, break the finish at the gaps to allow any trapped solvents to be released and then reapply a new coating recommended by the finish manufacturer. Resand
the area of the floor affected if necessary.
To help prevent WLS, be sure to address seasonal fluctuations and movement between boards. If these factors are unavoidable, use a less-elastic finish to minimize the effects. Opt for an aziridine 2-component finish rather than an isocyanate 2-component
finish, because it is less likely to cause issues. We recommend using StreetShoe® NXT and GymShoe®. Do not apply
a more elastic finish on top of a less-elastic one. Always use a sealer before applying a finish to help wood boards separate so there is a cleaner break of the finish. We recommend using VersaSeal™,
Hydroline® Sealer, Raw™ Sealer, or Lock N’ Seal™.
For fast drying stain, apply Basic Coatings® HyperTone™ Stains. HyperTone Stains
are ready to walk in as little as 30 minutes, while oil-based stains can take up to 24 hours to dry. Unlike oil-based stains, HyperTone Stains are non-flammable and safer for yourself and your customers. Read more about the dangers of oil-based stains and the benefits of waterbased.
Using the right finish or stain and maintaining the environment’s conditions will help prevent WLS from occurring. If you have questions about how to prevent or fix White Line Syndrome, please click here to fill out the online form, and your Basic Coatings Regional Manager will reach out to you.
Source: NWFA’s “Problems, Causes, and Cures 2018”
Photo courtesy of NWFA’s Problems, Causes, and Cures (3rd Edition, 2018